Sustainable features benefit remote Alaska prison.The mechanical system for the facility is designed to meet three main requirements: uninterrupted year-round service, super-efficient performance and full tamper resistance.
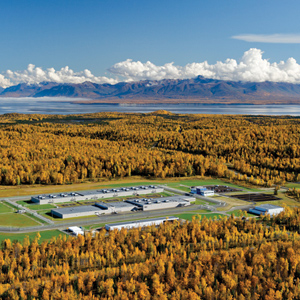
“Where could they possibly go if they got out?” asks one local, referring to prisoners at the new Goose Creek Correctional Facility in Alaska. Miles of thick forest and deep, cold water separate the prison from Anchorage.
The medium security prison is Alaska’s largest by far, housing more than 1,500 inmates. It’s a $240 million Alcatraz in the middle of a spruce and lichen sea. If an inmate were to make it past the 800 surveillance cameras, armed guards and 12-ft. fence topped with razor wire, among his sure-bet companions would be ornery moose and angrier mosquitoes.
Aside from its remote location in the Matanuska-Susitna (Mat-Su) Borough, Goose Creek has another feature that sets it apart from many of the newer prisons in the United States today - its Spartan-like atmosphere. Each cell contains only a steel desk, a bunk bed and a storage container.

Btu on lockdown
“This is one of the largest vertical construction projects that’s ever taken place in Alaska,” Mat-Su Borough Purchasing Officer Russ Krafft says. “It was like building an entire university campus all at once.”
The mechanical system for the facility is designed to meet three main requirements: uninterrupted year-round service, super-efficient performance and full tamper resistance.
Anchorage-based Superior Plumbing and Heating was tapped for the installation. The firm is part of the five-company Superior Group, one of the largest mechanical firms in the 49th state. “We retrofit and service correctional facilities, but Goose Creek was our first new construction prison project,” Superior General Manager Mark Erickson notes.
In true Alaskan spirit, the new facility is equipped with a no-nonsense hydronic system to heat the three largest buildings on campus. The general housing, support and visitation and vehicle maintenance buildings account for 435,000 sq. ft. of conditioned space.
Two smaller buildings - located more than 300 ft. from the central plant - have stand-alone systems. The outside administration building and warehouse each has a pair of 1-million Btu boilers. The mechanical systems in the complex are designed around a -23°F design temperature.
The system’s central plant - as formidable a creation as the prison itself - occupies two stories in the support and visitation building. From there, 3- and 6-in. pipes run underground to general housing and under the concertina wire to the vehicle maintenance building. Heavily insulated pipes are trenched 10 ft. below grade – well below the 5-ft.-deep frost line.
“It was a major coordination effort,” Erickson says, “especially being 75 miles from the shop.” Seven foremen were on-site for the duration of the project. When things were in full swing, there were 50 plumbers and pipefitters, 20 sheet metal workers and five office staff at Goose Creek every day. That’s in addition to the other trades.

Challenges in the sub-arctic
“One of the biggest challenges we had was designing and building the system consecutively,” Erickson says.
He notes the initial concept design was a collaborated effort of two mechanical and electrical engineering firms. One of the firms, Anchorage-based Coffman Engineers, took over full design responsibilities at the midpoint of the design. Coffman has extensive experience designing facilities in the harsh sub-arctic climate.
“We took over at the 65% completion mark,” says Coffman Principal Mechanical Engineer Bill McNeal, P.E., who was assisted by Coffman team members Michel Sotura, P.E.; Brent Little, P.E.; and Augustino Bacher, P.E.“Our job was to ‘Alaskanize’ the system. It took a better building envelope and a more robust mechanical system than what had originally been envisioned.”
Much of Alaska is challenged not only with frigid winter temperatures but several other issues as well. Frequent and significant earthquakes are a harsh reality. Ash fallout from several nearby active volcanoes offers additional challenges. As if that’s not enough, silt is generated by glaciers, including the nearby Matanuska Glacier. Rocks and boulders grinding against bedrock create a fine dust that goes airborne in high winds. The silt and ash require the ventilation systems to be equipped with good air filtration.
“The central boiler plant and pumping systems are configured with redundant or reserve units in order to ensure heat is always available,” McNeal says. “The natural gas-fired equipment also has an on-site propane reserve system good for two weeks of winter operation. The reserve fuel is necessary in the event that an earthquake interrupts the natural gas pipeline to the site. The reserve power generation system also has redundancy and a two-week fuel supply.”
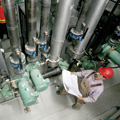
Hefty hydronics
“Due to the project’s fast pace, and Alaska’s short construction season, they were already trenching pipe while we were completing the design of the plumbing and other underground systems,” McNeal notes.
Appearing more like a master plan for a futuristic superhighway, the piping layout for Goose Creek shows the branching network from 12 natural gas-fired Aerco Benchmark boilers. The main boiler room took roughly a year to pipe. The best way to get the boilers to serve the numerous buildings and loads was to use an extensive primary-secondary system.
An 8-in. primary loop connects all condensing boilers, each equipped with a Taco KV3009 pump and 2-hp motor. Two 6-in. secondary loops tee off; one goes to the support and visitation building and the other to general housing. Inside the buildings, the large secondary loops feed heat exchangers for radiant floor loops, VAV boxes and air handlers. In addition, several flat-plate heat exchangers tap the glycol loop to heat large indirect water heaters.
When the mercury drops, the heat load is daunting – even though the buildings are well-insulated. This past winter saw ambient temperatures dip as low as -30°F, with severe winds and record snowfall. Most elements of the hydronic heating system are designed for a 40 °F delta T to lower the flow and conserve pumping energy.
“The large delta T also is needed for optimum efficiency from the condensing boilers,” McNeal says. “In addition to the high initial delta T, the return heating water is cascaded through radiant floor systems, as well as snow-melt piping in order to lower it even further to enhance the condensing at the boilers.”
To heat the concrete structures, several delivery methods are used. Haakon constant-volume hydronic air handlers heat the cell blocks. A 6-ft. swath of radiant tubing in the slab knocks out perimeter chill in cells situated against exterior walls.
The rest of the conditioned space has Greenheck VAV boxes to deliver ventilation and heat, and fin-tube baseboard is used in several locations. Snow melt in outdoor recreation areas, loading docks and sidewalks uses 14 miles of 5/8-in. Uponor PEX tubing. A 50/50 glycol/water mixture protects the pipe from freezing.
Gang showers, a laundry and a kitchen that prepares nearly 5,000 meals a day draw copious amounts of domestic hot water. In addition to the indirect tanks, Aerco Smart Plate indirect water heaters are installed remotely at numerous points throughout the prison.
Given the sheer quantity of water and numerous loads calling on the system, there had to be ample room for fluid expansion, thus three, 260-gallon Taco expansion tanks are tied into the system.
Heavy metal
With a large piping system and given the amount of time material was exposed during installation, a quality air and dirt separator was a necessity, especially at start-up.
Proctor Sales’ Troy Nibert supplied a 12-in. inlet, 4900 series air and dirt separator and boiler vent. The Benchmark boilers use 46 ft. of 22-in. Schebler vent. All water heaters and smaller stand-alone boilers vent individually, but with the same AL294C material.
Nibert adds the secondary hydronic loop uses Taco KS6011 pumps with 25-hp motors. To shrink floor space for each pump, a suction diffuser is used on the inlet side of the pump and a 6-in. multipurpose valve is located on the discharge side. Taco multipurpose valves act as a check, plug and balancing valve, while the suction diffusers eliminate the need for long, straight pipe runs on either side of the pump.
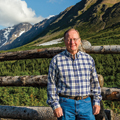
Good conduct
The prison is designed with sustainability in mind - not for the glamour of going green - but rather to keep operating and maintenance costs low and taxpayers happy. The heat never turns off in the prison. A temperature of 70°F is considered balmy in July, which leaves the building calling for heat overnight. In addition to the space-heating needs, significant amounts of domestic hot water are still required. The prison isn’t going anywhere anytime soon, so the ROI for quality products has time to mature.
The hydronically heated ventilation system utilizes Haakon energy recovery ventilators to assure stray Btu aren’t wastefully dumped into the frigid air outside. One ERV is used on each of the five housing groups within the general housing facility. HRV units for the laundry and kitchen are located in the central plant.
By default, the prison uses low-flow water fixtures. Plumbing fixture manufacturers in the prison include the likes of: American Standard, Sloan, Chicago Faucets, Elkay, Belvedere, Delta, Eagle, Fiat, Lasco, Haws, Halsey Taylor, Mustee, Woodford and Josam.
For reasons of security and energy efficiency, the cast-in-place walls include a thick layer of insulation and heavy steel grid. The grid is welded together at 6-in. centers and is integrated into all the walls, floors and ceilings.
By design, any opening in a wall more than 8 in. in dimension is barred off with super-hardened steel. How hard? Enough to require the use of 12,000 hacksaw blades to make it through just one bar. All other buildings on the prison campus are steel-framed with well-insulated steel-panel construction.
Cooling is rarely needed at the prison, and only in certain areas. Computer and server rooms and other electrical spaces that require cooling are handled by split-system direct expansion units. A central chiller plant cools adjacent areas in the support and visitation building that houses vocational education, dining room and medical areas.
The state of Alaska took a no-nonsense approach building the new prison. The engineering upgrade insisted upon by Coffman Engineers and Superior Plumbing and Heating’s workmanship met the challenge to produce a rock-solid system.
With the regular maintenance the system is sure to receive, both the prison and its mechanical equipment will remain in service for many years to come.