Biomass-fired boiler adds to University of Missouri’s sustainable footprint.
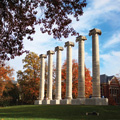
The University of Missouri – Columbia and its construction team are celebrating the completion of a milestone, two-year project aimed at significantly reducing the campus’ carbon footprint while propelling the university forward in its sustainability goals.
The design and construction team, which includes Overland Park, Kan.-based design engineer Sega Inc., and the construction manager at-risk - a joint venture between St. Louis-based McCarthy Building Co., and Chesterfield, Mo.-based CB&E Constructors - completed construction in December on a $75 million biomass boiler project at the campus power plant.
The 100% biomass-fired Babcock & Wilcox boiler, expected to be in service early this year, will be annually fueled with more than 100,000 tons of regionally supplied and sustainably sourced biomass. This new biomass boiler, along with the co-firing of biomass in the plant’s stoker boilers, is expected to reduce the university’s use of coal by more than 25%.
“The power plant upgrade was a very complex and highly technical project that presented many challenges to the team,” McCarthy Project Manager Mark Smith says. “The work was executed within a fully operational, combined heat and power facility that provides continuous utility services to the campus. Ongoing, uninterrupted plant operations came second only to safety on the project.”
Sega Project Engineer Adam Ross adds: “It was definitely a challenging, yet rewarding project. The coordination efforts by all parties were essential to the success of the project, and everyone worked well together to address the challenges encountered during design and construction.”
MU’s combined heat and power plant supplies electricity, heating and cooling for more than 15 million gross sq. ft. of buildings, including three hospitals, a research reactor, several research facilities and laboratories, academic and administrative buildings, residential halls and athletic facilities. The plant, a 2010 Energy Star combined heat and power plant award recipient, is nearly twice as efficient as a conventional power plant because it simultaneously produces the thermal energy (steam for heating and cooling) and electricity for the campus.
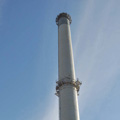
Getting the ball rolling
Realizing the growing importance of sustainability to students, faculty and staff, MU Chancellor Brady Deaton signed the American College and University Presidents’ Climate Commitment in 2009 and established the MU Sustainability Office. The current climate action plan sets a goal of reducing greenhouse gas emissions by 30% by 2016 and the new biomass boiler will help MU realize this goal. In addition to the new biomass boiler, MU installed in this project approximately 34 kw of solar panels (by Schott Solar), further demonstrating MU’s commitment to green energy and sustainability.
Since 2005, MU’s College of Agriculture, Food and Natural Resources and MU Extension have been dedicated to helping the power plant find the most cost-effective biomass fuel sources. Viable alternatives include burning corn cobs, switch grass and woody biomass from mill waste, development clearing and discarded pallets blended with coal. MU has co-fired biomass in its existing stokers under this program since 2006. With support from MU’s forestry department, it has developed some of the most comprehensive sustainability standards for forest-derived biomass incorporated in the biomass supply contract for the power plant.
The project included installing the new biomass boiler and a horizontal and vertical expansion of the existing boiler house, as well as structural restoration of two existing 325-ft.-tall, cast-in-place concrete chimneys. Also included was the complete replacement of the plant’s existing fuel unloading, handling and storage system.
Work to provide the new fuel systems included construction of a new fuel unloading and processing building and construction of five fuel storage silos and extensive conveyor systems, which allowed both biomass and coal handling on the same footprint. The first phase of the fuel project included the replacement of the coal system by constructing two under-silo coal conveyors that travel from the fuel receiving building to bucket elevators adjacent to the existing boiler house. Each conveyor system is approximately 250 ft. in length. Also included was the replacement of two over-bunker coal conveyors about 200 ft. long within the existing boiler house, as well as two vertical 80-ft.-tall “bucket” elevators.
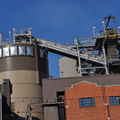
Keep it moving
In order to maintain full operations of the power plant during construction, temporary fuel handling and conveying systems were put in place to feed the remaining boilers while the existing systems were being replaced. The temporary systems provided MU with an uninterrupted supply of fuel, and therefore steam and electrical power for eight months of the project.
The construction sequence required the conveying equipment be put in place following foundation construction of the new fuel unloading and processing building. Plant operations required the coal system be put into operation as soon as it was in place, so the fuel building was built from the foundations up around and over the operating coal system.
“A project with this much complexity required special considerations through the planning, design and construction phases,” Ross says. “Installing the boiler and material-handling equipment as well as other auxiliary equipment into existing buildings and infrastructure required extensive coordination with vendors.”
To better coordinate layout and to minimize interferences, Sega used three-dimensional modeling throughout the design and construction of the project.

“The 3-D model was essential to these efforts. It allowed us to work with the vendors early on to establish layout parameters,” Ross says. “When updates or new information was received, we could quickly and efficiently react to the changing information and illustrate this to the university, McCarthy/CB&E and the subcontractors in the field. Having a 3-D model facilitated everyone’s review and ultimately allowed everyone to have buy-in before the revised drawings were sent to the field.”
Menasha, Wis.-based AZCO was the mechanical subcontractor for the installation of the new boiler and all the conveying systems. The tight schedule for the coal system replacement required innovative coordination within the operating power plant and significant shift work and overtime.
Fenton, Mo.-based Kaiser Electric was the electrical subcontractor on the project and played a critical role in successfully meeting a tight schedule. With the coal system component of the project on the fast track to beat the winter weather, Kaiser worked 30 electricians in two shifts, six days a week.
“We knew going into the coal system work that multiple shifts would be required in order to succeed,” Smith says. “AZCO and Kaiser Electric brought the manpower and resources to the project team required to execute an extremely difficult project in a very short period of time and keep the plant running without interruption. This was a critical step in the project and both subcontractors should be commended for their top-notch efforts.”
The second part of the fuel project included construction of the biomass fuel system. This system includes three storage silos and a system of conveyors and bucket elevators that parallel the fuel system from the unloading and processing building to the boiler house.
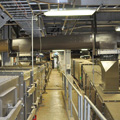
How the new biomass boiler works